Industrie 4.0: Revolution verschoben
Die umfassende Vernetzung der Produktion galt als großes Zukunftsversprechen. Doch die Umsetzung stockt. Bisher hat in Deutschland noch kein Unternehmen Industrie 4.0 komplett implementiert. Woran es hakt und wie sich die Herausforderungen bewältigen lassen.
Vor drei Jahren war es der große Hype: Industrie 4.0. Vernetzte Produktionsanlagen sollten die vorausschauende Wartung vereinfachen, die Produktivität steigern und die Herstellung von Produkten bis hin zur Losgröße 1 ermöglichen. Viele sprachen von einer vierten industriellen Revolution.
Doch die große Begeisterung ist längst abgeflaut. Zwar sind sich Unternehmen darüber bewusst, dass Digitalisierung und Vernetzung wesentliche Faktoren für ihre Wettbewerbsfähigkeit darstellen. Viele haben in den vergangenen Jahren auch digitale Technologien wie Big Data, Cloud Computing und Künstliche Intelligenz (KI) integriert. Doch insgesamt ist die vorhergesagte Revolution ins Stocken geraten. Laut einer Studie von Bitkom Research sehen 95 Prozent der deutschen Unternehmen Industrie 4.0 als Chance. Gleichzeitig stufen sich 66 Prozent als Nachzügler oder sogar als bereits abgehängt ein. Zu einem ähnlichen Ergebnis kommt eine Studie der Managementberatung Bearingpoint. Demnach hat bislang noch kein einziges Unternehmen hierzulande Industrie 4.0 komplett implementiert.
Woran liegt das? „Die größte Herausforderung ist für viele Unternehmen, dass die Digitalisierung in Produktion und Logistik nicht das einzige Thema ist, das angegangen werden muss“, sagt Melanie Tobler, Co-Autorin der Studie und Partnerin bei Bearingpoint. Auch wenn am Ende der Transformation viele Chancen stehen, müssen Projekte gestemmt und Investitionen getätigt werden, die kurzfristig Geld kosten und Ressourcen benötigen. „Hier sind es oft Priorisierungsentscheidungen, die Unternehmen aktiv zugunsten einer digitalen Zukunft und zugunsten der Smart Factory treffen müssten“, sagt Tobler.
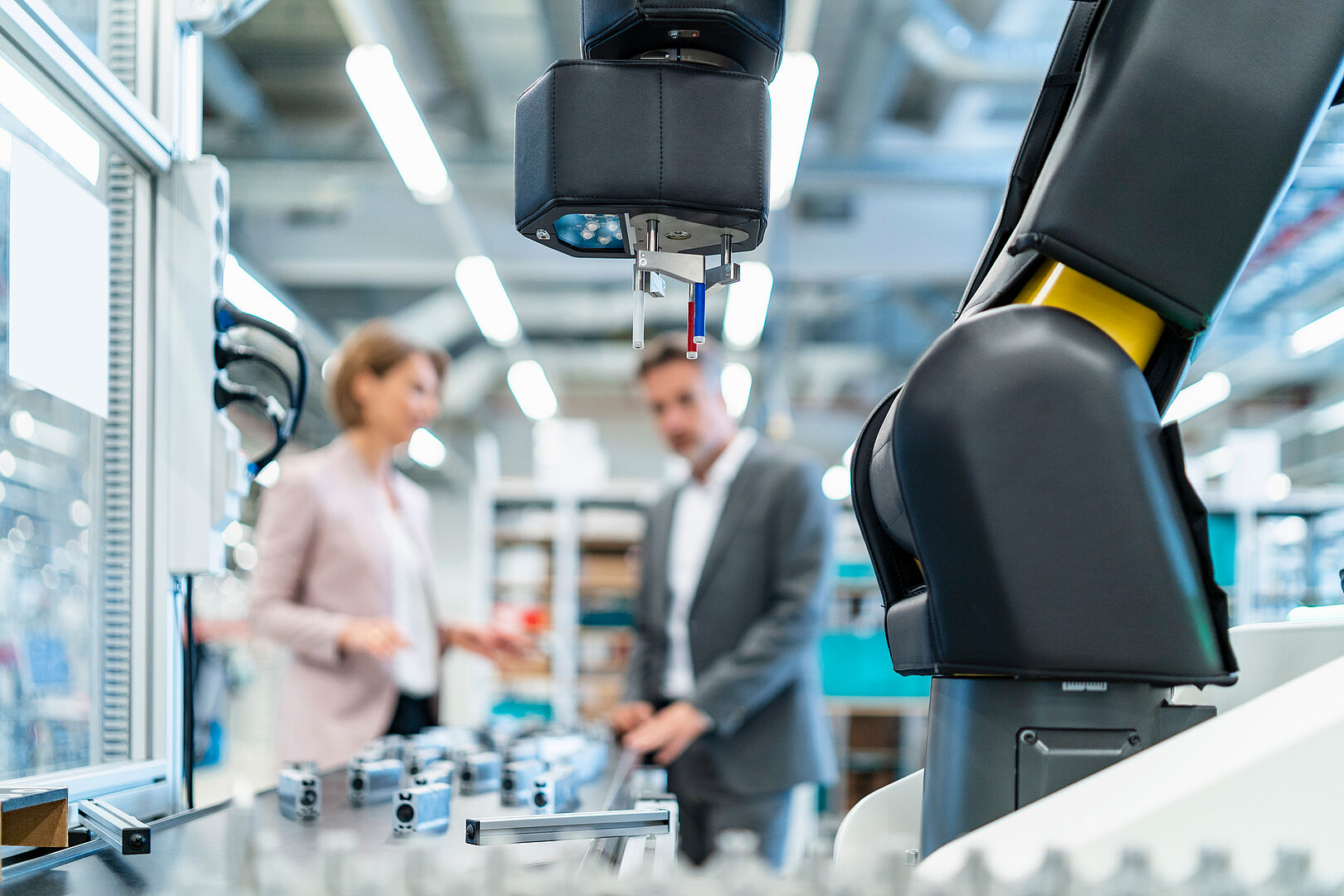
Vertrauen und Rechtssicherheit
Klar ist: Eine Umsetzung von Industrie 4.0 bedeutet für Unternehmen neben dem Einsatz neuer Technologien auch einen umfassenden Wandel des Geschäftsmodells, der Risiken birgt. „Ohne den Nachweis eines wirtschaftlichen Mehrwerts oder einer Effizienzsteigerung werden viele Unternehmen zögern, in diese Technologien zu investieren“, sagt Henrik Schunk, Vorsitzender des Lenkungskreises Plattform Industrie 4.0 sowie Vorsitzender des Verwaltungsrats des Spann-, Greif- und Automatisierungstechnikherstellers Schunk in Lauffen am Neckar. Das Netzwerk Plattform Industrie 4.0 strebt an, die digitale Transformation in der Produktion voranzubringen.
Konkret sieht Schunk drei Handlungsfelder, wie Industrie 4.0 doch noch zum Erfolg werden kann: Mittelständler benötigen eine mitarbeiterorientierte Digitalstrategie, ausreichende Ressourcen sowie die Unterstützung durch staatliche Förderprogramme, die die Einstiegshürden senken. Außerdem können staatliche Vorgaben dazu beitragen, dass Unternehmen einen klaren Rahmen erhalten, wie Industrie 4.0 praktisch umgesetzt werden kann, und sie bei der Nutzung dieser Technologien nicht ins Hintertreffen geraten.
„Auch wenn der Begriff Industrie 4.0 inzwischen weit verbreitet ist, bleibt das tatsächliche Wissen über die Inhalte und Möglichkeiten für viele Unternehmen begrenzt, sodass der Zugang zu fundiertem Knowhow eine Herausforderung darstellt“, sagt Schunk. Daher hat er die Initiative Next Level Mittelstand gestartet. Durch Schwarmintelligenz aus der Initiative sollen mittelständische Unternehmen die nötigen Werkzeuge und das Wissen an die Hand bekommen, damit sie schnell und effizient von den Vorteilen der Industrie 4.0 profitieren können.
Praxistaugliche Standards
Eine weitere Anlaufstelle für Unternehmen ist die Open Industrie 4.0 Alliance. „Die Einführung von Industrie 4.0 wird bei mittelständischen Unternehmen durch das Fehlen eines klaren Startpunkts erschwert, wodurch wichtige Grundlagen für die Digitalisierung fehlen. Hinzu kommen unvollständige Technologieeinführungen, die zu Unterbrechungen in Wertschöpfungsketten führen und eine effiziente Datenbereitstellung verhindern“, sagt Ekrem Yigitdoel, Geschäftsführer der Open Industry 4.0 Alliance.
Auch bei der Umsetzung der regulatorischen Anforderungen sieht Yigitdoel Optimierungsbedarf. „Beispielsweise könnten staatlich geförderte Handreichungen Orientierung bieten und die Umsetzung erleichtern. Ein vereinfachter grenzübergreifender digitaler Daten- und Wissensaustausch sowie klare, praxisnahe Standards würden dazu beitragen, die Prozesse effizienter zu gestalten und Hürden für Unternehmen abzubauen“, sagt er. Aber auch mangelhafte Investitionen in die digitale Infrastruktur, wie die Breitbandversorgung und die schleppende Einführung von 5G-Netzen, bremsen den Einsatz fortschrittlicher Technologien. Und nicht zuletzt hemmen die Energiekosten und Unsicherheiten in der Energieversorgung die Investitionsbereitschaft der Unternehmen. „Besonders Technologien wie Big Data oder Künstliche Intelligenz, die eine hohe Rechenleistung und damit viel Energie erfordern, leiden unter diesen Unsicherheiten“, stellt Yigitdoel fest. Was den Mangel an Fachkräften und spezialisiertem Wissen betrifft, ließe sich dieser durch enge Zusammenarbeit und durch den Know-how-Transfer in Umsetzungsgemeinschaften, wie der Open Industry 4.0 Alliance oder der Initiative Next Level Mittelstand, beheben.
Der Bearingpoint-Studie zufolge hat Deutschland beim Thema Industrie 4.0 schon an vielen Stellen eine hervorragende Ausgangsbasis, denn es hat Prozesse digitalisiert, die an anderen Standorten in der Welt heute noch viel manueller laufen. „Die Chance, mit Innovationen, Automatisierung und digitaler Intelligenz im weltweiten Standortvergleich hohe Lohnkosten wettmachen zu können, müssten wir schleunigst nutzen“, sagt Studienautorin Tobler. Einzelne Vorreiter zeigen, dass das geht. Die breite Masse muss aber noch beweisen, ob die Pilotprojekte und Digitalisierungsinitiativen auch flächendeckend in die Betriebe ausgerollt werden können.
An Vorbildern orientieren
Neben Konzernen wie Siemens und Bosch, die hierzulande führend bei Industrie-4.0-Lösungen sind, gibt es auch familiengeführte mittelständische Unternehmen, die schon bedeutende Fortschritte gemacht haben. Dazu zählen etwa Trumpf, Festo und Phoenix Contact. Diese Unternehmen dienen als Vorbilder für den Mittelstand und zeigen mit ihren Lösungen, wie Industrie 4.0 erfolgreich implementiert werden kann. Das Unternehmen Schunk strebt ebenfalls an, Pionier bei Industrie-4.0-Lösungen zu werden. „Es ist wichtig, dass immer mehr kleine und mittelständische Unternehmen ermutigt werden, sich auf diesen Weg zu begeben“, sagt Schunk.
Einer der Vorreiter, das mittelständische Technologieunternehmen Phoenix Contact, sieht aktuell die größte Herausforderung bei der vollständigen Einführung von Industrie-4.0-Lösungen in der nahtlosen, barrierefreien Datenlogistik – analog zum Beispiel der Güterlogistik, wo durch die Einführung des genormten ISO-Containers die Kosten des globalen Gütertransports deutlich gesunken sind. „Die fehlende barrierefreie Datenlogistik verhindert derzeit in vielen Fällen eine Disruption von Wertschöpfungsprozessen und Geschäftsmodellen“, sagt Christoph Kelzenberg, Director Digital Innovations & Director Operational Excellence bei Phoenix Contact in Blomberg.
Die Experten sind sich einig: Damit Industrie 4.0 zum Erfolg wird, gilt es, technologische, regulatorische und infrastrukturelle Hürden zu überwinden. Die Zusammenarbeit von Unternehmen, Politik und Wissenschaft ist wichtig, um die Transformation zu beschleunigen. Mit mehr Innovationskraft und Kooperation könnte Deutschland seine Wettbewerbsfähigkeit langfristig sichern und sich sogar als Vorreiter etablieren.
Quelle: Magazin "Creditreform"
Text: Iris Quirin
Bildnachweis: Getty Images
Wir sind für Sie da: Creditreform vor Ort
Wir sind für Sie da:
Creditreform vor Ort
Sie haben Fragen zu unseren Produkten und Lösungen? Wir beraten Sie gerne. Finden Sie hier Ihren persönlichen Ansprechpartner.