Gebrauchtes wie neu
Die Industrie trimmt ihre Ressourceneffizienz. Das betrifft nicht nur den Einsatz von Rohstoffen, sondern auch Produktionsanlagen. Immer mehr Unternehmen hauchen älteren Maschinen ein zweites Leben ein. Warum dieses sogenannte Remanufacturing sowohl ökonomisch als auch ökologisch sinnvoll ist.
Millionen Tonerkartuschen und Tintenpatronen werden jedes Jahr gekauft, genutzt, bis sie leer sind und dann weggeworfen. Es werden Fabriken und Lagerhallen gebaut und wieder abgerissen, wenn sie nicht mehr gebraucht werden. Und Maschinen- und Anlagenbauer? Die stellen Motoren, Kräne und Pumpen her, die irgendwann ausgedient haben – und bauen dann neue.
In Deutschland werden jährlich rund 1,3 Milliarden Tonnen Rohstoffe verbraucht. Aluminium und Stahl, Kupfer, Lithium und viele andere. Das sind fast 16 Tonnen pro Bundesbürger. Diese Zahlen des Naturschutzbundes Deutschland verdeutlichen das Maß der Ausbeutung bestehender Ressourcen durch eine Wirtschaft, die noch immer fast ausschließlich auf Verbrauch ausgerichtet ist. Doch es tut sich was: Immer mehr Unternehmen bemühen sich, die bisher vorherrschende lineare Struktur durch eine zirkuläre abzulösen. Stichwort: Kreislaufwirtschaft.
Der Weg zu einer optimalen Weiternutzung gebrauchter oder defekter Produkte, Maschinen oder Anlagen ist für viele Betriebe allerdings noch weit. Hilfreich sind Zwischenstopps. Dazu zählt die Reparatur. Defekte Baggerschaufeln, Bohranlagen oder Spritzgussmaschinen werden wieder betriebsfähig gemacht. Oder Refurbishing. Das ist eine qualitätsgesicherte Überholung und Instandsetzung, um ein Produkt, eine Maschine oder Anlage wiederverwenden und erneut vermarkten zu können. Einen noch größeren Schritt machen Unternehmen mit Remanufacturing. Das Prinzip: Durch Wiederaufarbeitung werden gebrauchte Maschinen und Komponenten wie neu.
Zu diesem Zweck werden nach einer kompletten Demontage alle Bauteile gereinigt und genau untersucht. Was nicht mehr funktionsfähig ist, wird durch Neues ersetzt.
Ist das noch gut oder kann das weg?
So macht es beispielsweise die Dortmunder Maschinenbaufirma Wilo unter dem Leitspruch „Vermeidung und Verwendung vor Verwertung und Entsorgung“.
In Recycling-Center des Pumpen- und Pumpensystemherstellers werden zurückgekommene defekte Produkte sortenrein zerlegt und die Teile, die während der Betriebszeit keinem Verschleiß unterliegen, repariert oder wieder in Neuprodukte eingebaut. „Rund 30.000 Bauteile halten wir so jährlich im Kreislauf“, sagt Thomas Fetting, Group Director Analysis, Repair & Recycling bei Wilo.
Häufig bringen Wiederaufbereiter das Objekt auf den neuesten Stand der Technik und versehen es mit der gleichen Gewährleistung wie für ein Neuprodukt. Gregor Grandl, Senior Partner bei Porsche Consulting und verantwortlich für den Bereich Maschinen- und Anlagenbau, lobt eine solche Bearbeitung mit dem Ziel, die Effizienz der Objekte zu steigern, als „ökonomisch und ökologisch sinnvoll“. Er berichtet von einem Werkzeugmaschinen-Hersteller, der 40 Jahre alte Anlagen seiner Kunden zurückholt, sie zerlegt, aufbereitet und beim Wiederzusammenbau mit neuer Software versieht: „Die mechanischen Prozesse der Maschinen bleiben gleich, die digitalisierte Steuerung wird modernisiert.“ Nach dem Motto „Pimp my machine“ werden auch veraltete Drehbänke, 3D-Drucker oder Wärmepumpen erneuert. „Gut erhaltene, wertvolle Teile einer in die Jahre gekommenen Maschine werden so erhalten.“
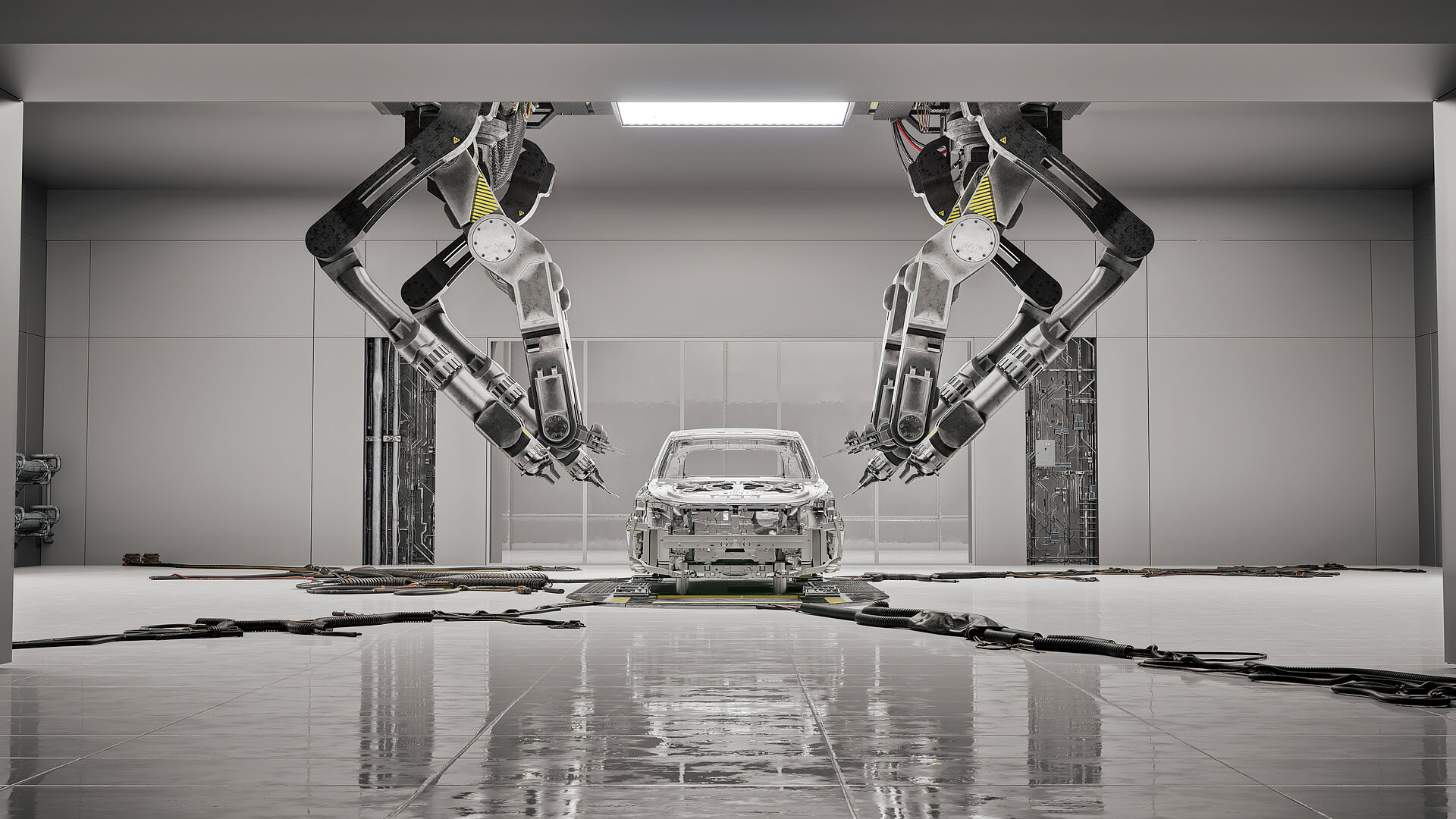
Second Hand spart bares Geld
Als Remanufacturing-Pionier gilt die Firmengruppe Liebherr, die seit 30 Jahren Wiederaufarbeitung betreibt. Aktuell sind das an 15 Standorten rund 7.500 Komponenten vom Turbolader bis zum Zylinderkopf. Das Familienunternehmen bietet seinen Kunden an, in die Jahre gekommene Komponenten der Bagger, Radlader oder Mining Trucks aufzuarbeiten. Jens-Christian Wannenwetsch, kaufmännischer Leiter der Firma Liebherr-Ettlingen (160 Mitarbeiter), die seit 2004 die europäischen Reman-Aktivitäten der Gruppe leitet: „Die meisten Kunden aber bestellen bereits aufgearbeitete Komponenten aus einem unserer Zentrallager und schicken ihre Cores erst zurück, wenn die benötigte Reman-Komponente bei ihnen eingetroffen ist.“ Die Wiedermontage der wiederaufgearbeiteten Teile gleiche der Serienmontage: „Bei Motoren beispielsweise arbeiten wir in einer getakteten Linienproduktion.“
Nach Fertigstellung und einem Prüfstandlauf, bei dem die gleichen Qualitätskriterien angelegt werden wie in der Serienfertigung, werden die erneuerten Komponenten lackiert, verpackt und ausgeliefert. Sie kosten den Kunden „deutlich weniger“ als ein Neubauteil, betont Wannenwetsch: „Inklusive der Vergütung für das Altteil spart er zwischen 25 und 30 Prozent, bei einigen Bauteilen sogar bis zu 50 Prozent.“ In der Liebherr-Kasse landen aus dem Business jährlich rund 350 Millionen Euro. Die Aufarbeitung gebrauchter Komponenten sichere zudem die langjährige Ersatzteilverfügbarkeit: „Das hat eine enge Kundenbindung zu Folge, generiert Umsätze weit über den Maschinenverkauf hinaus und schafft auch die Basis für weitere Maschinenverkäufe.“ Damit nicht genug: Der Erhalt massereicher Bauteile helfe, nachhaltig zu wirtschaften: „Wir sparen allein im Logistik- und Produktionsprozess verglichen mit der Neuteilfertigung rund 65 Prozent CO2.“
Auch der Automobil- und Industriezulieferer Schaeffler hat eine Tochter, in der die Wiederaufbereitungsaktivitäten gebündelt sind: die Schaeffler Industrial Remanufacturing Services in Wuppertal. Hier werden Wälzlager – sie dienen im Maschinen- und Gerätebau als Fixierung von Achsen und Wellen – auf ein zweites Leben vorbereitet. Das spart sowohl CO2-Emissionen als auch Ressourcen, wie das Beispiel eines Kunden zeigt, bei dem regelmäßig vier große Pendelrollenlager ersetzt werden müssen. Remanufacturing-Leiter Ingo Schmidt erklärt: „Nutzt er ein wiederaufbereitetes Lager statt einer Neuproduktion, reduzieren sich die CO2-Emissionen um bis zu 95 Prozent und die Kosten um 70 Prozent.“ Außerdem verkürzten sich Wartungsdauer und Stillstandszeiten. Ähnlich ist es bei Lokomotiven und Waggons durch die Aufbereitung gebrauchter Bahnlager.
Alte Idee gewinnt neue Bedeutung
Mit Blick auf die Historie von Liebherr und Schaeffler sagt Thomas Neumann vom unabhängigen Borderstep Institut: „Die Wiederaufbereitung von Produkten, Maschinen und Anlagen ist nichts Neues, gewinnt aber angesichts knapper und teurer werdender Ressourcen an Bedeutung, insbesondere dort, wo viele hochwertige Teile verbaut werden.“ Laut Anna Trawnitschek vom Deutschen Institut für Normung (DIN) sind Branchen wie Luft- und Raumfahrt, Medizintechnik und Automobilbau dafür besonders geeignet: „Je komplexer Maschinen und Anlagen sind und je hochwertiger die Bauteile, desto größer ist der wirtschaftliche Anreiz für die Hersteller, diese zurückzunehmen und wiederaufzubereiten.“ Ihr Institut hat 2023 für zirkuläre Prozesse den Standard DIN SPEC 91472 entwickelt.
Laut dem Borderstep Institut lassen sich durch die Wiederaufbereitung gebrauchter Produktkomponenten im Schnitt etwa 75 Prozent Rohmaterial und Energie einsparen. Außerdem sei Remanufacturing aufgrund neuer EU-Richtlinien zur Nachhaltigkeitsberichterstattung von Unternehmen ein gutes Verkaufsargument. Das sagt auch Felix Prumbohm, Referent für Produktion, Lean Management sowie Entwicklung und Konstruktion im Verband Deutscher Maschinen- und Anlagenbau (VDMA): „Betriebe, die wiederaufbereitete Maschinen, Anlagen oder Produkte sowohl anbieten als auch einsetzen, verkleinern ihren ökologischen Fußabdruck. Das ist gut für die Wettbewerbsfähigkeit und zahlt sich durch günstigere Konditionen auch auf dem Kapitalmarkt aus.“ Er nennt noch einen Pluspunkt: „Gerade in Zeiten, in denen Lieferketten wenig stabil und bestimmte Rohstoffe und Bauteile schwierig zu bekommen sind, sichere ich mir durch den Rücklauf gebrauchter Komponenten meine Produktionsbasis.“ Dieses Argument findet sich auch im „VDMA-Leitfaden zu zirkulären Geschäftsmodellen“, der Verbandsmitgliedern zur Verfügung steht.
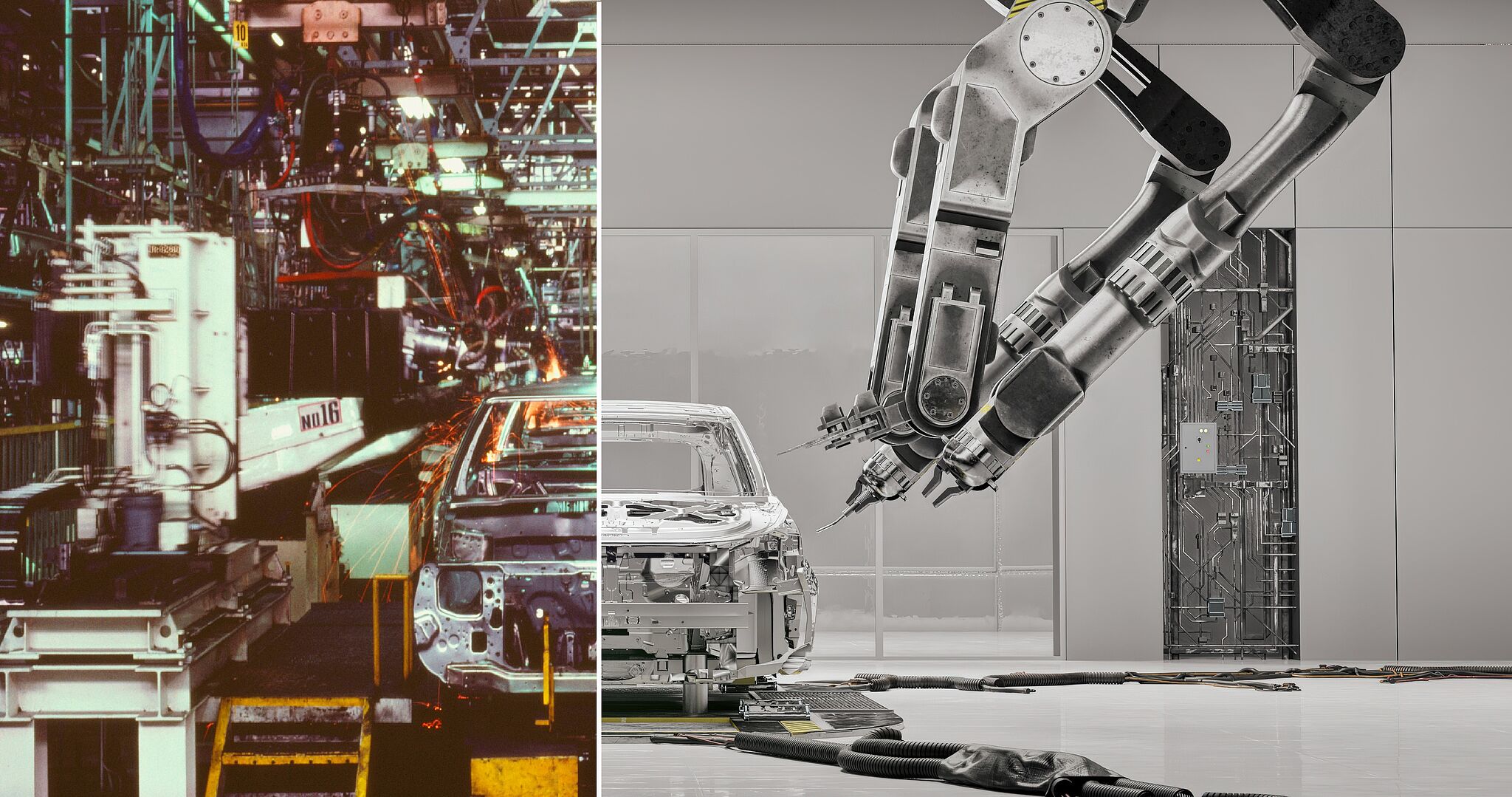
Remanufacturing beginnt beim Design
Wie Thomas Neumann hält Felix Prumbohm Remanufacturing für einen wichtigen Baustein einer guten Kreislaufwirtschaft. Dafür müssten die Hersteller Rücknahmesysteme aufbauen und bereits in der Produktentwicklung „eine einfache Demontage und Wiederaufbereitung mitdenken“. Auch Gregor Grandl, Senior Partner bei Porsche Consulting und verantwortlich für den Bereich Maschinen- und Anlagenbau, empfiehlt Herstellern, die mit Remanufacturing Geld verdienen wollen, beim Design ihrer Produkte zu beginnen: „Wenn ich weiß, dass ich eine Maschine oder Anlage später einmal zerstörungsfrei demontieren möchte, um noch brauchbare Teile herauszufiltern, sollte ich schon bei der Produktion besser etwas verschrauben als verschweißen und idealerweise standardisierte Komponenten verwenden. Eine solche Gestaltung eines Produktes, einer Maschine oder Anlage ist zudem ein Verkaufsargument.“
Bei ZF in Friedrichshafen weiß man das. „Design for Sustainability“ heißt dort die Direktive, mit der schon in der Produktentwicklung die Grundlagen für ein späteres „zweites Leben“ der Fahrzeugteile gelegt werden. So sollen idealerweise nur noch korrosionsbeständige Werkstoffe sowie Verbindungstechniken, die eine beschädigungsfreie Demontage ermöglichen, verwendet werden. Laut Bereichsleiter Tomasz Galazka vermeidet ZF durch Remanufacturing jährlich mehr als 32.000 Tonnen CO2-Emissionen: „Bei der Aufarbeitung von gebrauchten Fahrzeugteilen lassen sich bis zu 90 Prozent der Rohstoffe einsparen, die für die Herstellung eines Neuteils benötigt werden.“ Auf die Qualität und Leistungsfähigkeit der Komponenten könnten die Kunden sich verlassen, „denn wir bringen sie immer auf den aktuellen Serienstandard“. Deshalb gilt auch die gleiche Garantie wie für neue Teile. Die ZF-Division Aftermarket bietet 5.500 wiederaufgearbeitete Kfz-Ersatzteile an – vom Bremssattel über Lenksysteme bis zu Automatikgetrieben. Philippe Colpron, Leiter ZF Aftermarket, ermutigt die Werkstätten, aktiv wiederaufgearbeitete Teile anzubieten und die Altteile zurückzugeben, „denn echte Kreislaufwirtschaft kann nur gelingen, wenn wir alle zusammenarbeiten“.
60 bis 70 Prozent gerettet
Die familiengeführte Brose-Gruppe beliefert rund 30 E-Bike-Hersteller mit mechatronischen Systemen und elektrischen Antrieben. Im Werk in Berlin-Moabit wird gebrauchten Motorbauteilen, etwa Hohlwellen, Drehmomentsensoren und Steckerbuchsen, ein zweites Leben eingehaucht. Die Antriebe werden von Servicetechnikern per Hand demontiert und gereinigt. Dann wird jedes Teil überprüft. Entspricht die Qualität noch den Brose-Vorgaben, wird das gebrauchte Bauteil mit neuen Komponenten zu einem Reman-Drive „verheiratet“, wie Vincent Bahar es nennt.
Der Leiter des Remanufacturing-Programms ist stolz: „Wir können 60 bis 70 Prozent aller Bauteile retten und wiederaufbereiten.“ Dabei spare man im Vergleich zur Produktion mit Neuteilen rund 50 Prozent CO2-Emissionen. Die Qualität eines wiederaufbereiteten Antriebs ist laut Bahar genauso gut wie die eines neuen Serienprodukts: „Deswegen geben wir auch die gewohnte Gewährleistung von zwei Jahren.“ Der Anteil der wiederaufbereiteten Antriebe am Gesamtgeschäft macht bisher zwar weniger als zehn Prozent aus, aber die Nachfrage steigt. So hat der britische Sharing-Anbieter Beryl für seine City-E-Bike-Flotte gerade die größte Lieferung in der Geschichte des Remanufacturing-Programms erhalten. Bahar: „Es gibt Monate, in denen die Nachfrage so groß ist, dass wir mit der Produktion kaum hinterherkommen.“
Quelle: Magazin "Creditreform"
Text: Jürgen Hoffmann
Bildnachweis: Glowimages / Gettyimages